How to Implement an Autonomous Maintenance Program
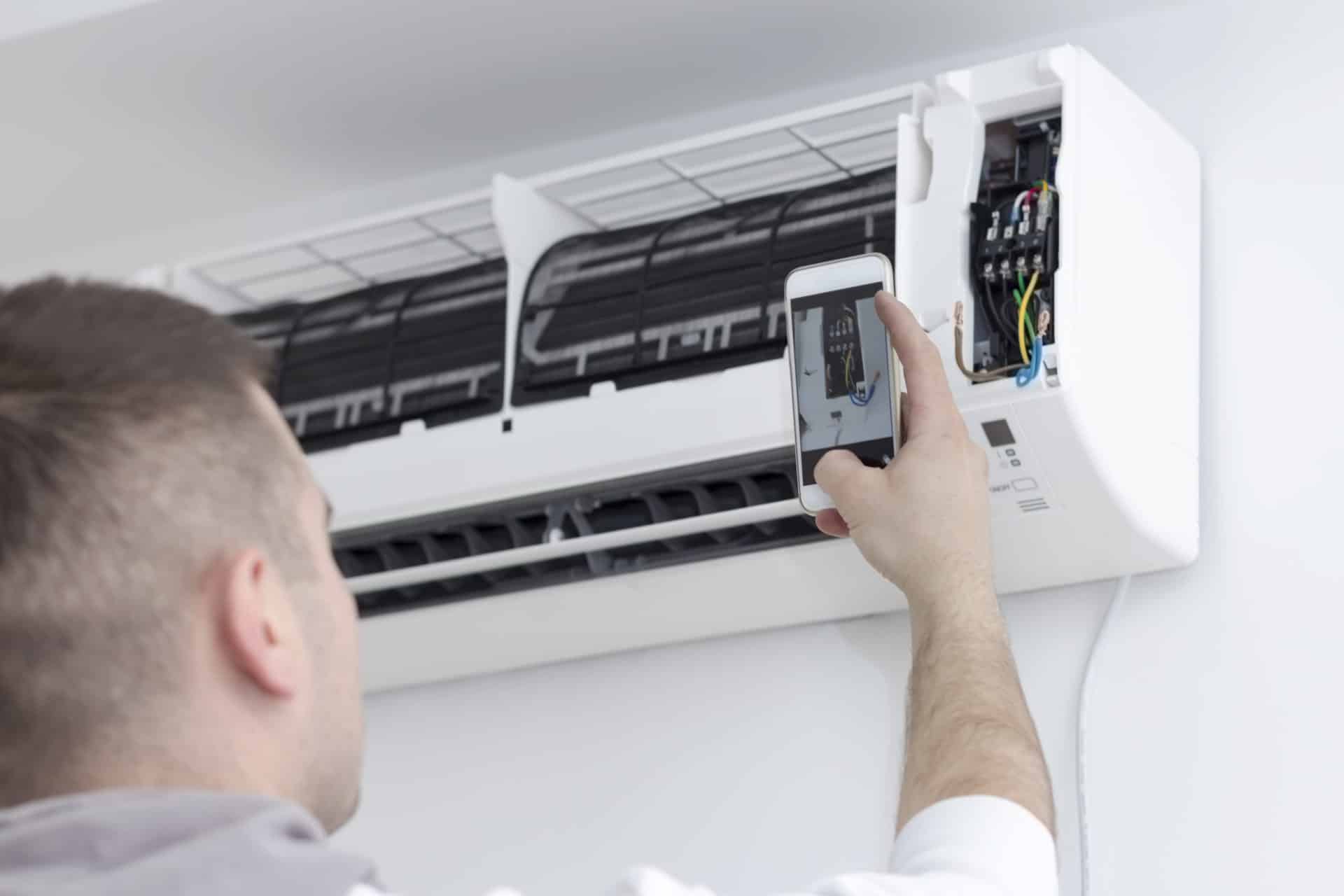
Learn what autonomous maintenance is, how it supports TPM and lean manufacturing, and how to empower frontline teams.
Autonomous maintenance (AM) can significantly streamline your preventive maintenance tasks. You can spend less time allocating maintenance resources to all the equipment in your facility. AM can also lessen the amount of maintenance needed when specialized maintenance staff perform routine tasks.
However, given the nature of AM, improper implementation is a big risk. If machine operators aren’t trained correctly, the system can inadvertently do more harm than good. For this reason, you must thoroughly research AM and how to implement autonomous maintenance before adding it to your maintenance strategy.
Key Takeaways:
- Autonomous maintenance (AM) involves training machine operators to handle routine maintenance tasks and detect early equipment issues.
- This maintenance strategy enhances overall equipment performance, which helps improve production output.
- Operators gain more comprehensive knowledge of the machines they manage through maintenance training.
- Shifting simple maintenance work to operators helps lighten the workload for skilled technicians, giving them more time for complex repairs.
- Clear roles, structured reporting, and additional operator time are needed to implement autonomous maintenance successfully.
What Is Autonomous Maintenance?
Autonomous maintenance assigns basic maintenance tasks to machine operators instead of depending only on maintenance staff. Essentially, operators handle routine upkeep, while trained technicians manage complex tasks.
This practice is a core aspect of a total productive maintenance (TPM) program. It results in a lighter workload for your maintenance technicians, allowing you to allocate more resources to more complex work.
However, leaving preventative maintenance tasks to people who aren’t trained as maintenance technicians carries risks. That’s why properly implementing autonomous maintenance is so important.
How Does Autonomous Maintenance Work?
Operators receive structured training to recognize and address early signs of equipment issues during normal operations. Once trained, operators can perform minor maintenance tasks that help sustain equipment reliability.
This structured approach helps organizations fully take advantage of the benefits of preventive maintenance. When operators consistently provide basic care to their own equipment, it will further prevent equipment deterioration, improve safety, and minimize unexpected failures.
Maintenance activities that are often shifted to machine operators in an autonomous maintenance program include:
- Initial machine cleaning
- Lubricating moving parts
- Tightening bolts, fasteners, and fittings
- Initial cleaning of work areas
- Checking for abnormal noise, vibration, or temperature
- Recording task completion and equipment condition
Key Benefits of Autonomous Maintenance
Fewer Equipment Breakdowns
Operators conduct regular inspections, cleaning, lubrication, and minor adjustments before small issues escalate. As a result, equipment runs more reliably, and downtime is reduced. Properly managing these tasks will also enhance your overall equipment effectiveness (OEE).
Improved Uptime & Productivity
Autonomous maintenance minimizes unscheduled downtime and supports more consistent throughput. Machines operate with fewer disruptions, and production schedules stay on track. These benefits enhance your overall operational efficiency.
More Engaged Frontline Workers
Giving machine operators ownership of basic maintenance builds knowledge, skill, and accountability. Workers take more pride in keeping equipment running well, which contributes to better teamwork and higher job satisfaction.
Lower Maintenance Costs
When operators take responsibility for some mundane maintenance tasks, they’ll reduce their reliance on expensive emergency repairs and prolong equipment effectiveness. This will also allow skilled maintenance staff to focus on more complex work, resulting in lower overall operational costs.
Better Root Cause Identification
Operators monitor equipment closely and share their findings with your maintenance team. You’ll identify problems earlier, which gives your team more time to investigate the root cause of the issue. Once the root cause is detected, it’s easier to perform maintenance tasks that prevent reoccurrence.
Autonomous Maintenance vs. Traditional Maintenance
Autonomous Maintenance | Traditional Maintenance | |
Primary Responsibilities | Operators handle routine tasks such as cleaning, inspection, and minor adjustments. Maintenance technicians focus on complex repairs. | Dedicated maintenance technicians handle all maintenance activities. |
Training Requirements | Operators receive training in basic maintenance, equipment care, and condition monitoring. | Operators conduct production work only, so they receive no maintenance training. |
Cultural Mindset | Shared responsibility for routine maintenance between operators and maintenance staff. | A clear division of labor where maintenance teams own maintenance processes and operators focus on production targets. |
Equipment Knowledge | Maintenance training can increase operator knowledge of optimum equipment conditions. | Operators only know as much about their equipment as they need to know for production. |
Collaboration | Highly collaborative process between maintenance and operational teams. | Limited interaction between operators and maintenance staff. |
Continuous Improvement | Ongoing improvement efforts involve operator feedback. | Continuous improvement is typically driven by the maintenance team alone. |
Examples of Autonomous Maintenance Tasks
Various production equipment requires various maintenance tasks. Here are some examples of preventive maintenance tasks that you can assign to your operators based on equipment type.
Computer Numerical Control (CNC) Machines
- Clean guide rails and work surfaces daily to prevent debris buildup
- Inspect and replace worn tool inserts
- Check and top up lubrication oil levels
- Clean cooling fans and air filters to prevent overheating
- Monitor spindle performance for unusual noise or vibrations
Conveyors
- Clear accumulated dust or product residue from belts and rollers
- Inspect belts for wear or misalignment
- Apply lubrication to moving parts as described in the manufacturer’s specifications
- Identify and report loose hardware or unusual noises
Injection Molding Machines
- Clear mold surfaces of residue that could affect product quality
- Inspect hydraulic lines for leaks or wear
- Check and maintain coolant levels
- Inspect and clean ejector pins
- Record process parameters to detect gradual changes
Packaging Machines
- Clean sensors to reduce the risk of false readings
- Inspect sealing jaws and cutting blades for damage
- Remove product residue from contact surfaces
- Check pneumatic hoses for leaks
- Verify proper operation of photo-eyes and counting devices
8 Steps to Implement Autonomous Maintenance
1. Clearly Define Roles & Responsibilities
It’s best practice to give machine operators autonomous maintenance activities related to the equipment they run each day. They already know how these machines work, so they will have a good starting point when it’s time to train them on proactive maintenance. It’s also important to set a clear inspection schedule in advance. This schedule will tell operators when to service their equipment based on their training.
2. Train Operators on Specific AM Tasks
Your maintenance personnel are best suited to show your operators how to perform maintenance tasks and determine which maintenance processes are too complex or sensitive for non-maintenance staff to handle. Proper training by experienced maintenance technicians helps operators complete these tasks correctly, avoid damaging the equipment, and stay safe.
3. Start Small With a Pilot Machine
Start your program with just one machine or line to test the process first. Doing so will help you refine your process before applying it to more equipment. Starting small also gives you a chance to check for any quality issues and refine your ideal maintenance schedule before the full rollout.
4. Dedicate Time for Operators to Perform AM Work
Operators need extra time to complete maintenance tasks correctly. This time should be scheduled in addition to their normal production work. Maintenance work cannot be rushed or squeezed in between their regular duties. Rushed maintenance increases the risk of poor maintenance.
5. Standardize Visual Maintenance Management
Use clear visual aids like color coding, labels, standard operating procedures (SOPs), and one-point lessons to help make maintenance steps easier to follow. These tools will help operators independently manage tasks more confidently.
6. Establish a Simple Issue Reporting Process
Operators are very familiar with their machines, which is why they are good at spotting early signs of potential equipment failures. However, they shouldn’t try to resolve problems other than what they were trained to do. That’s why you also need to set up an easy way for them to report issues to your maintenance team.
7. Share Maintenance Data
Give your operators key data about their equipment’s performance to help them see how their efforts make a difference. It also helps them understand where more maintenance is needed or where improvements can be made. Sharing this data also supports lean maintenance strategies by encouraging targeted maintenance work.
8. Continuously Improve AM
Sustaining autonomous maintenance requires continuous improvement. Conducting regular kaizen events is a good way to implement a continuous improvement process. A kaizen event is a short-term brainstorming session that targets a specific challenge and enhances an existing process. Run these events with your operators and maintenance technicians. They will help you find better ways to maintain equipment and reduce the chance of future failures.
Best Practices for Autonomous Maintenance Success [Checklist]
- Perform Daily Operator Checks
Assign operators to inspect equipment at the start of each shift to detect issues early. - Pair With a CMMS
Log all inspection results, minor fixes, and observations into your computerized maintenance management system (CMMS) or software tool to track trends. - Use Visual Cues
Apply labels, marks, and color coding on equipment to guide cleaning, lubrication, and inspection. - Standardize Work Procedures
Document clear, repeatable procedures for routine maintenance tasks to improve consistency. - Train Operators Regularly
Provide regular training on equipment functions, basic maintenance, and problem identification to continuously build skills. - Promote Cleanliness
Establish routine cleaning as one of your regular maintenance tasks to reduce contamination. - Hold Quick Daily Huddles
Hold short team meetings regularly to review results, discuss issues, and determine future goals. - Conduct Periodic Reviews
Regularly assess your autonomous maintenance process to drive continuous improvement.
Empower Your Maintenance Teams with ServiceChannel
After you successfully implement autonomous maintenance, you need to manage it. The right technology can help your team perform maintenance tasks more efficiently.
ServiceChannel provides a user-friendly preventive maintenance management solution.
Our platform can help you track inspection reports and resource allocation, as well as assist with inspections, monitoring data, and much more.
Request a demo today!